Controls

Controls
Varspe
All our controls are compatible with the entire Var-Spe product and model catalogue, and allow for different work management functions and different work modes to guarantee a wide choice depending on the application situations and the specific environment requirements.
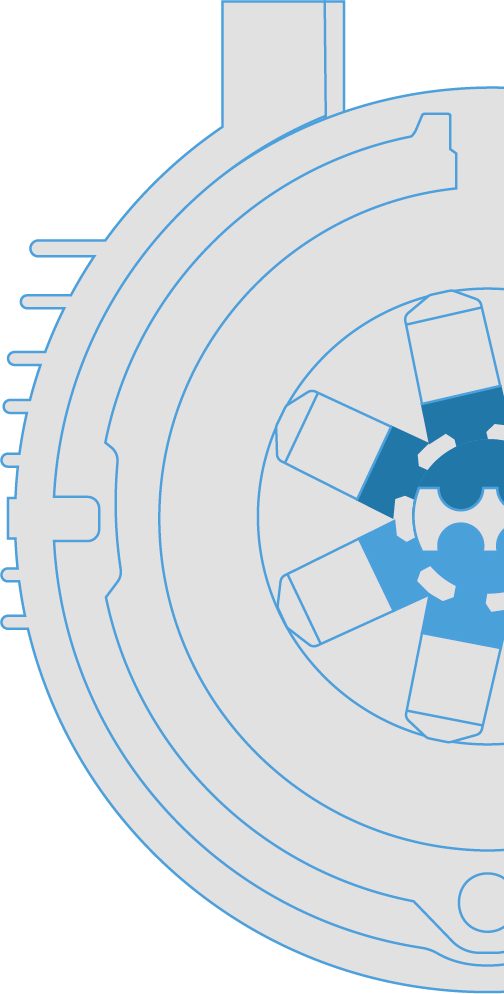
This is a standard control which ensures accurate and sensitive speed regulation through the tull range with minimum operating torque.
By means of a oair of bevel gears, an orthogonal differentiation orientable through 360° has been obtained from the normal shaft of the regulation pin, which permits the manual regulation of the speed .under all positions and the extension of a small shaft to a certain distance i necessary.
K SERIES
This lever control operates over approximately 90° degrees from maximum re verse to forward. It has a friction clutch to adjust the amount of force required to stroke it and will stay in place when set. Also, it is possible to rotate the lever to several other positions. There is about 5 degrees of deadband in the control on either side of the center zero position. Force required to strike the end of the lever is shown in the table below.
Performance is the same as previous control code 02, but it is possible to make frequent transitions: about 1000 per hour. It is also a available in a flanged version (Code 03F) to mount some other devices such as a chain sprocket, for example. È identico per prestazioni al due precedenti comandi, soltanto non c’è alcun gioco intorno allo zero.
HEAVY SERIES
It allows to obtain a variable output shaft speed on the variator according to the resistance torque. The control is ideal for application like winders because the speed automatically decreases according to the increasing of the reel diameter and to the correspondingperipheral speed. This allows to wind at a controlled tension with ratio 1:6 between the minimum and the maximum diameter. In order to get lower or higher tension values, it is necessary to make manual regulations on the hanwheel. To have the regulation on the other sense of output rotation is sufficient to reverse the input sense of rotation
K SERIES
This control was expressly designed for those applications requiring an automatic speed reduction in relation to the present load at the variator end. This need was felt particularly in winding applications (wires, belts), where the contemporary keeping of tension and feed speed – that is the output power – is requested. The control code 07 designed for K series variators, keeps constant power for a speed ratio equal to 1/6, that is from 1450 rpm to about 250 rpm.
K SERIES
Il comando elettrico permette la regolazione a distanza, tramite pulsantiera (non inclusa), da zero al massimo dei giri, in entrambi i sensi di rotazione.
È costituito da un motorino elettrico, monofase o trifase, e da un riduttore a vite senza fine. It’s possible to manually adjust the speed control shaft. The regulation time, max-0-max, is about 30÷34 seconds.
This control has the same features of the control code 20 except the speed adjustment time which is approximately 2 minutes.
HEAVY SERIES
This control was designed to exploit the digital electronics (PLC or Personal Computer) already existing inside the customer’s machine.
It is sufficient to have an electronic system with 2 digital outputs and an input for the feedback signal.
The control is able to run infinitive speed levels and can be both single and bi-directional, as a function of the feed-back signal.
K SERIES
This control allows to adjust proportionally speed of variator by a potentiometer lever or by external analogue electric signals.
0÷5 or0 ÷ 10 Valt-DC and/or 0 ÷ 20 or 4 ÷ 20 mA.
in the simple version, feedback signal to electronic aduster is given by the potentiometer (fitted on the variator) which takes control of the movement. Regulation is a loop type with continuous control of variator and output speed of the unit is proportional to control signal. On request, feedback signal can be given by a speedometer dynamo (DT) connected to output shaft of variator. This way, revolution stability also in presence of important load variation is assured, since signal depends on output shaft speed. Direction of rotation of output shaft has to be stated when placing order.
This control has the same performances as code 37. It is provided with a second solenoid valve (H) and when disenergized, it allows mechanical zeroing of the output shaft.
This control allows an accurate manual regulation of variator in one direction of output shaft only. Il is equipped with a hydraulic device which sets variator to zero automatically at each stop of motor and starts it gradually at preset speed at an adiustable time from 2 to 10 seconds (flow control). The use is recommended in strong inertia motorization. Direction of rotation of output shaft has to be stated when placing order.
This control consists of a little three-phase ratiomotor incorporating two remote limit microswitches operating control shaft in one direction of rotation only.
This control is equipped with the same automatic zero setting device as code 46 for duty in strong inertia motorization.
HEAVY SERIES
The control allows remote adjustment of the number of revolutions of the variator on the basis of a compressed air signal.
It is useful to solve the problems of speed variation in sundry industrial applications, with pneumatic control signals ranging from 0,2 to 1 bar (3÷15 psi).
With a stationary speed variator, this control allows manual presetting of two speeds, one for each direction of rotation. Hence, by exciting alternately the electrovalve solenoids it is possible to obiain a programmati variation in the number of revolutions up to the preset speeds and consequently reversing of motion: it solenoids are not excited, the variator will automatically set itself to zero revolutions.
K SERIES
Same performances of control cade 65 but does not allow zeroing of variator. Zeroing is assured only if one of the ring nuts is at zero speed excluding in this way one sense of rotation.
K SERIES
With this control it is possible to make remote variations of speed through push-buttons (same conditions of the remote electric control code 20): furthermore it permits automatic zeroing every time the motor stops, conditioning the driven machine to start at zero revolutions every time. This control is also provided with two external fiow controls one for each direction of rotation: these flow controls permit variation of control response times according to desired acceleration and deceleration rales.
K SERIES
This control is similar to code 67 and allows rapid zeroing through a pashbutton and automatic zeroing e every time the motor stops, besides it permits regulation of speed in both directions of rotation with optional accelerations and decelerations. Solenoid SA must be energized for the control to operate. The auxiliary zeroing feature is not intended to be used as an emergency shutdown it merely overrides any preset ramps.
K SERIES
The control sinchronizes two speeds (primary and secondary). Power factor correction is replaced by this control. The Synchronizer Control is mainly used on Packaging Machines (Flow Pack Systems). The control is used to keep the label and bags in a central position compared to the bag length.
The control has two input controls:
one by handwheel setting the feed or the package lenght, the second utilises a piloted impulse to a solenoid valve from proximity switches or from a photo-electric cell.
This latter signal allows the handwheel setting to be increased or decreased to ensure the label position in the middle of the bag.
K SERIES